Activated Carbon: A Widely Used Adsorbent Material In Industrial Applications
Activated carbon—often derived from renewable coconut shells—is one of the most versatile and widely used adsorbents in modern industry. Known for its extremely high surface area, porous structure, and excellent chemical stability, activated carbon (also referred to as activated charcoal) has found applications ranging from water and air purification to precious metal recovery and chemical processing. In this guide, we detail the key properties, manufacturing processes, and most significant industrial applications of activated carbon, with a focus on coconut shell activated carbon.
Catalog
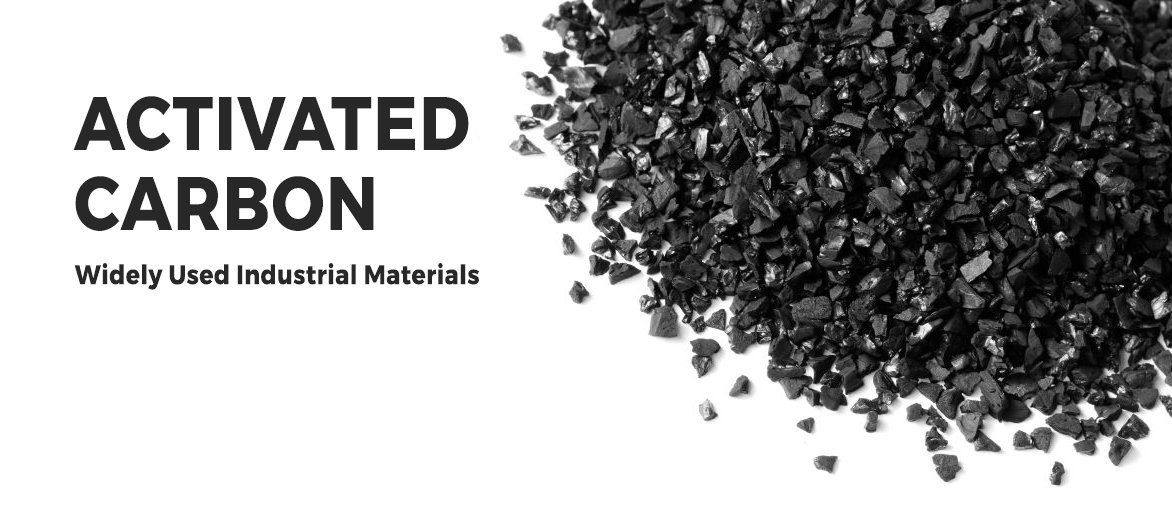
Overview and Key Properties
Activated carbon is produced by a process that “activates” a carbon-rich precursor to create an extensive network of micropores, mesopores, and even macropores. This structure results in a phenomenal surface area—often exceeding 1,000–1,200 m²/g for quality coconut shell products—and grants the material its renowned adsorption capabilities. Key properties include:
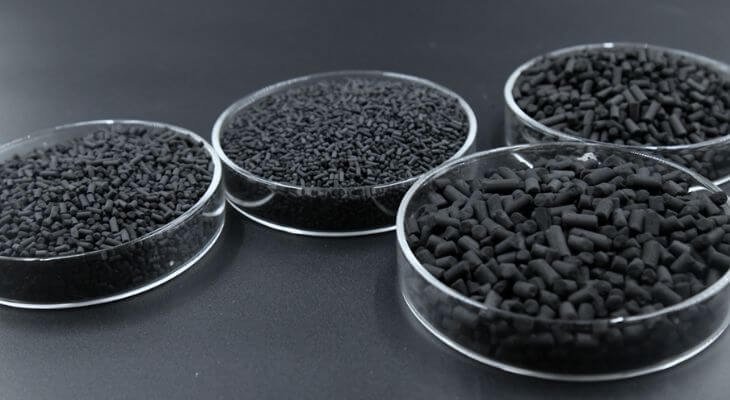
High Surface Area and Porosity: The microporous structure (over 80% of pores in many coconut shell carbons) provides vast active sites for adsorption. This is ideal for capturing small molecules and industrial pollutants.
Chemical Inertness: Activated carbon is highly resistant to chemical attack by acids, bases, and corrosive gases, ensuring long-term stability in harsh industrial environments.
Mechanical Strength: Especially when produced from coconut shells, the material exhibits superior hardness and low dust generation. This durability is crucial for filtration systems subject to abrasion and high flow rates.
Renewability: Sourced from coconut shells—a renewable agricultural byproduct—this activated carbon is an eco-friendly alternative to coal or wood-based carbons.
These characteristics collectively enable activated carbon to efficiently remove impurities, decolorize solutions, and capture volatile compounds in many industrial processes.
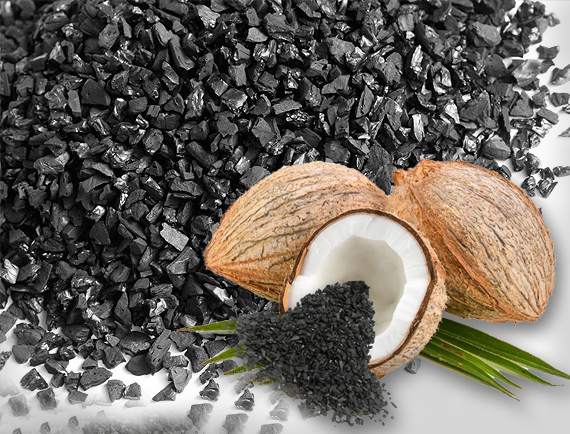
Manufacturing Process
The production of high-performance activated carbon involves several key steps:
1. Raw Material Preparation
Coconut shells are thoroughly cleaned, dried, and crushed to remove any extraneous fibers and impurities. This step ensures a uniform precursor for subsequent processing.
2. Carbonization
The prepared coconut shells are subjected to pyrolysis in a low-oxygen atmosphere at temperatures typically between 500–600°C. This step converts the raw material into basic charcoal by removing volatile compounds while forming a carbon matrix.
3. Activation
To develop an extensive porous structure, the carbonized material undergoes activation. This is usually done using a physical (steam) or chemical method (KOH or phosphoric acid). In steam activation, temperatures range from 800°C to 1,000°C, which enlarges existing pores and generates new ones. Chemical activation often occurs at lower temperatures and can tailor the pore-size distribution. The result is activated carbon with high micropore volume and a well-balanced pore structure suited for industrial uses.
4. Finishing and Quality Control
After activation, the carbon is washed to remove residual chemicals, then dried and milled to the desired particle size. Quality control measures—such as BET surface area analysis, iodine number, and hardness tests—ensure the activated carbon meets stringent performance criteria for industrial applications.
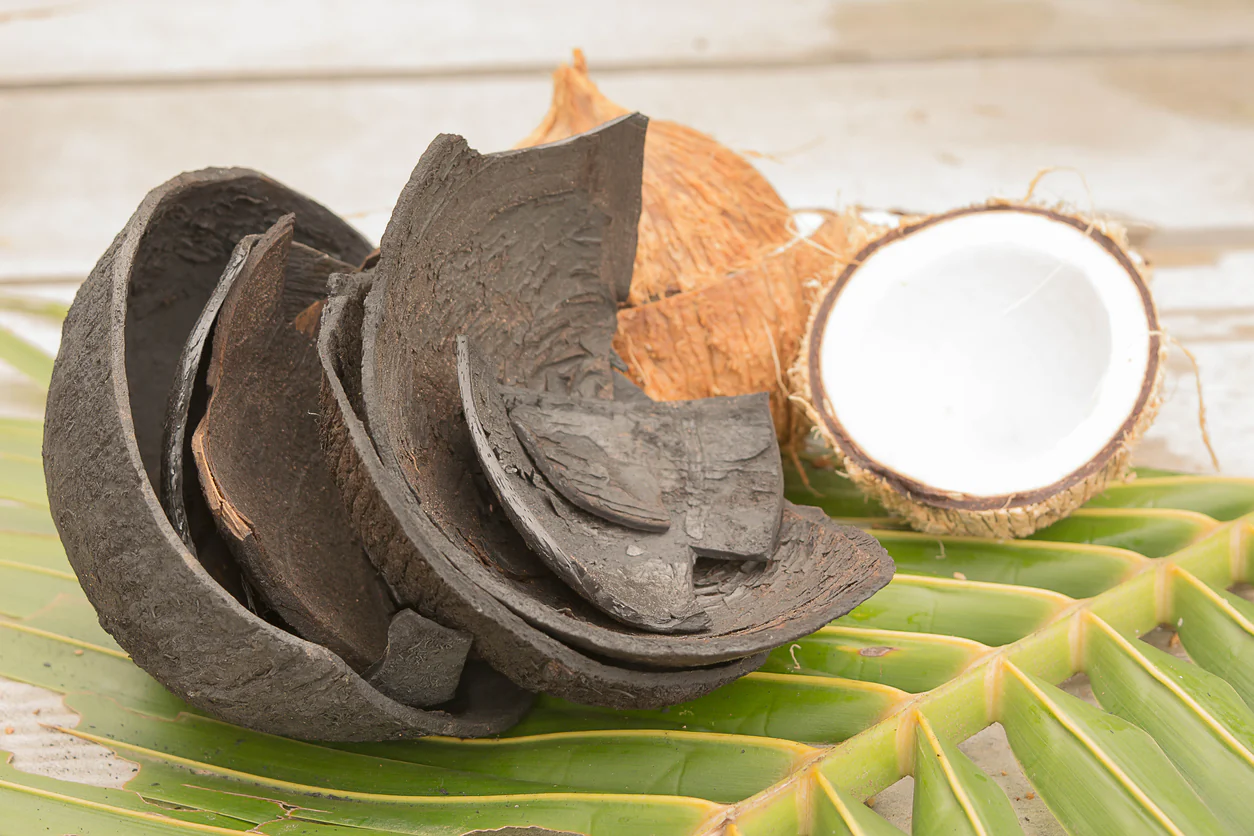
Industrial Applications
Activated carbon’s exceptional adsorption ability and durability make it indispensable across numerous industrial sectors. Below are the key areas of application:
1. Water and Wastewater Treatment
Activated carbon is widely used in water treatment plants to remove organic contaminants, chlorine, and taste-and-odor compounds. In industrial wastewater systems, it adsorbs pollutants ranging from pesticides to dissolved organic matter, thus ensuring compliance with environmental regulations. Granular activated carbon (GAC) derived from coconut shells is especially popular because of its high micropore content and low ash levels, which improve filtration efficiency and prolong filter life.
2. Air and Gas Purification
For industrial air purification, activated carbon removes volatile organic compounds (VOCs), odors, and harmful gases from exhaust streams. Its porous structure makes it an effective trap for airborne contaminants in manufacturing facilities, chemical plants, and even in gas masks. In addition, it plays a role in solvent recovery by adsorbing residual organics from vapor streams, reducing emissions and enabling recycling of valuable compounds.
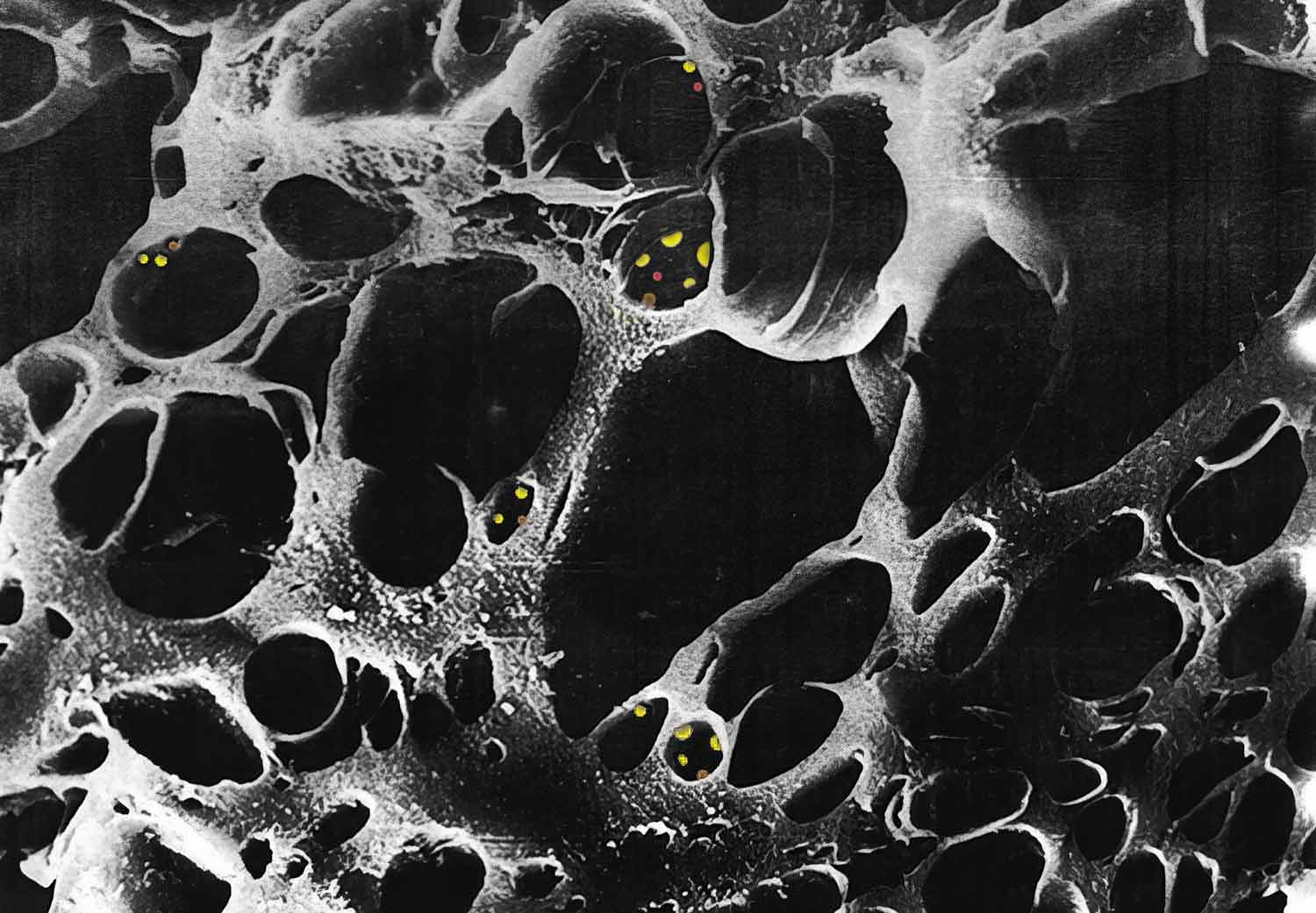
3. Precious Metal Recovery
In gold and other precious metal recovery processes, activated carbon is used to adsorb metal complexes from cyanide leach solutions. Coconut shell activated carbon is favored for this application because its high activity and excellent hardness yield superior performance in the rigors of gold extraction. By efficiently capturing soluble gold complexes, it ensures higher recovery rates and improved economic viability.
4. Chemical Processing and Catalysis
Activated carbon serves as a catalyst support in many chemical reactions, thanks to its high surface area and inertness. In industrial chemical processing, it is employed to remove impurities from process streams and can also be chemically modified (e.g., impregnated with metals) to enhance catalytic activity. Its use in reactions such as oxidation, hydrogenation, and dechlorination helps improve product purity and process efficiency.
5. Industrial Air Filters and Odor Control
Industries concerned with indoor air quality or emission control install activated carbon filters in their ventilation systems. These filters adsorb organic vapors, reducing odors and harmful emissions. In high-demand settings such as manufacturing plants and refineries, coconut shell activated carbon is used because it offers consistent performance, low pressure drop, and long service life, all of which are essential for continuous operation in industrial air cleaning systems.
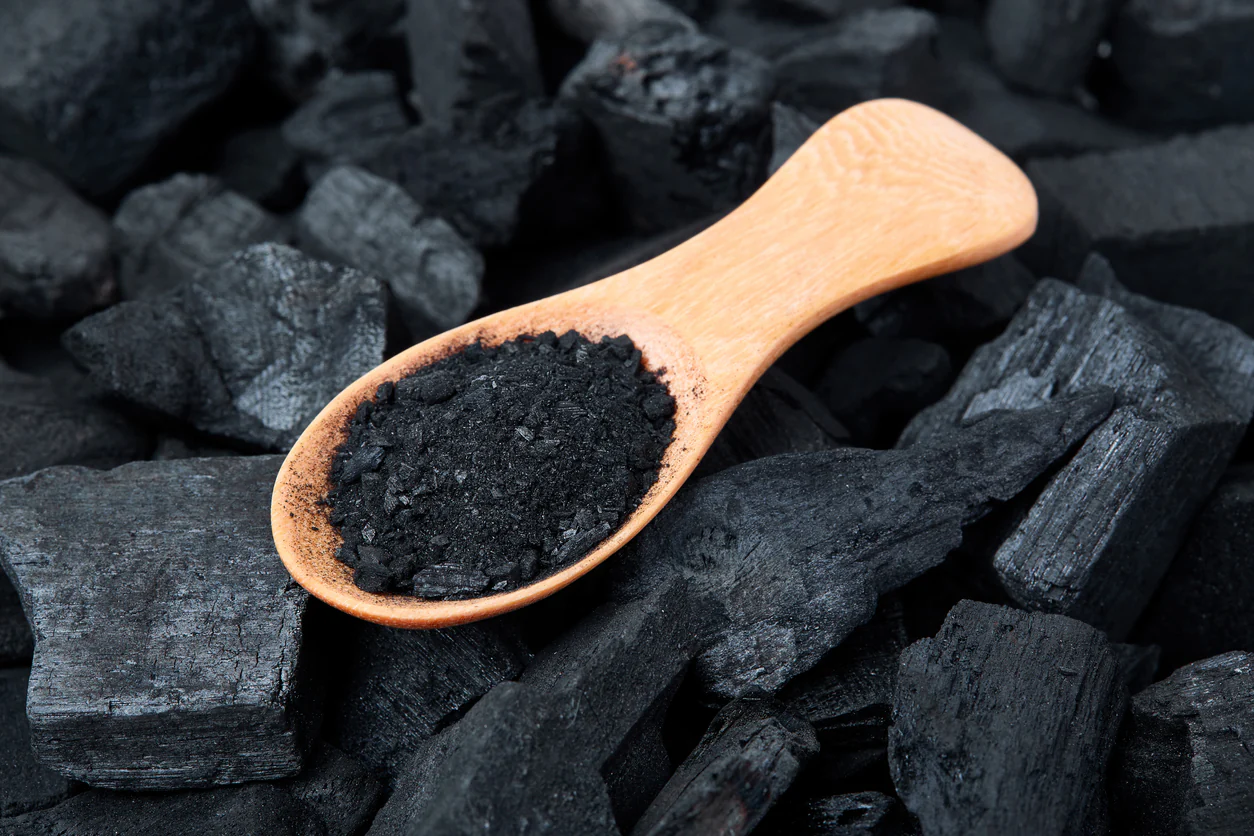
Safety and Handling Considerations
While activated carbon is chemically inert and generally non-toxic, proper handling is essential in industrial environments:
Dust Control: Fine carbon particles can become airborne; engineers use dust collection systems to minimize inhalation risks.
Storage: Activated carbon should be stored in dry, well-ventilated areas away from extreme temperatures and chemicals that might affect its adsorption properties.
Regeneration: In many systems, used activated carbon is regenerated via thermal treatment or chemical washing. Strict protocols must be followed during regeneration to handle any volatile adsorbed compounds safely.
Equipment Compatibility: Ensure that activated carbon does not react with any process chemicals, especially in systems where pH or corrosive agents are present.
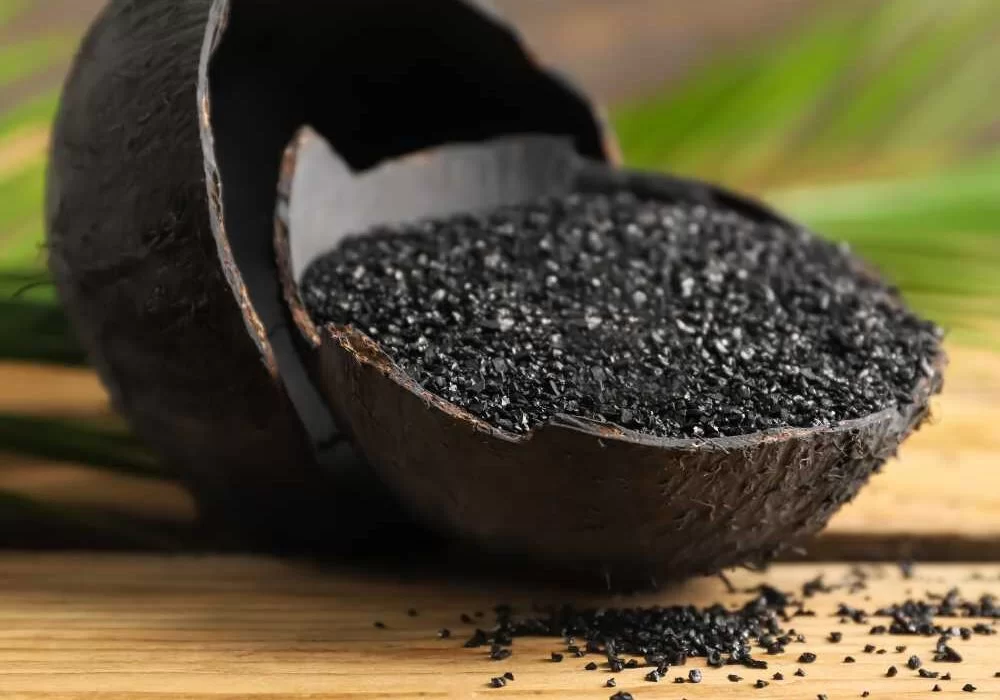
Conclusion
Activated carbon, particularly that derived from coconut shells, offers unmatched adsorption performance and is central to many industrial applications. Its high surface area, tailored pore structure, durability, and renewable origin make it an ideal material for water and air purification, metal recovery, chemical processing, and odor control. As industries pursue more sustainable and efficient processes, coconut shell activated carbon stands out as a key component in modern purification and environmental management technologies.
For more information or to discuss specific industrial applications, please feel free to contact at feronia@wit-stone.com | +86-15655559799.With rigorous quality controls and tailored grades, activated carbon continues to drive innovation in industrial filtration and purification systems.