How Sodium Sulfide is Used in Mineral Processing?
- FERONIAYANG
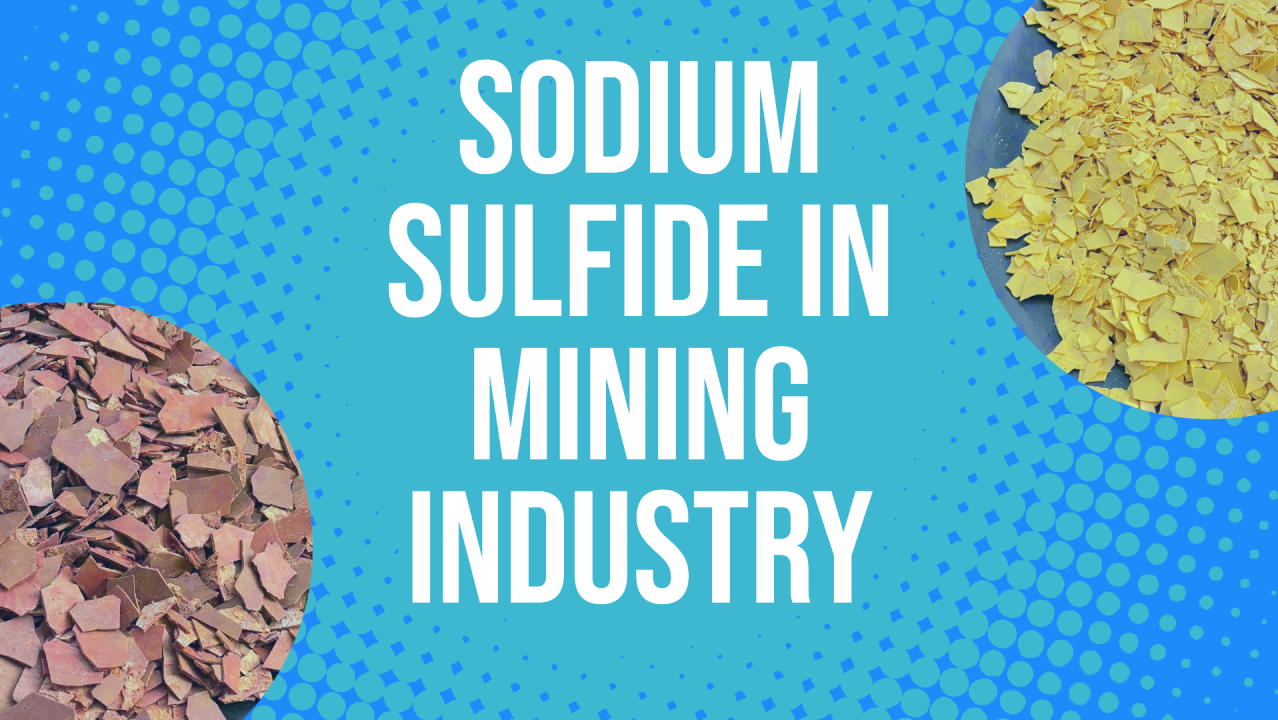
Sodium sulfide (Na₂S) is a crucial chemical product widely used in mineral processing, particularly playing a key role in flotation processes. Flotation is one of the essential techniques in mineral processing, enabling the effective separation of different minerals and the extraction of valuable metal components. In this process, sodium sulfide acts as both an activator and inhibitor and is used to treat oxidized ores, sulfide ores, and polymetallic ores, aiding in the efficient separation and recovery of minerals.
1. Mechanism of Sodium Sulfide in Mineral Processing
In mineral flotation, sodium sulfide is typically added to slurry containing oxidized ores to convert metal oxides into more floatable sulfides. Specifically, sodium sulfide performs two primary functions:
As an Activator: In some flotation processes, particularly for oxidized copper ores, sodium sulfide helps convert oxidized copper in the ore into copper sulfide, thereby increasing flotation efficiency. According to experimental data, adding sodium sulfide can significantly enhance copper recovery in oxidized copper ore treatment, with recovery rates typically reaching 80-90%.
As an Inhibitor: In the flotation of polymetallic ores, sodium sulfide can inhibit the flotation of certain undesired minerals, such as pyrite, thus enhancing the recovery of target metals. This is especially crucial in processing lead-zinc ores and copper ores. Research has shown that using sodium sulfide as an inhibitor can improve lead and zinc recovery rates by about 5%.
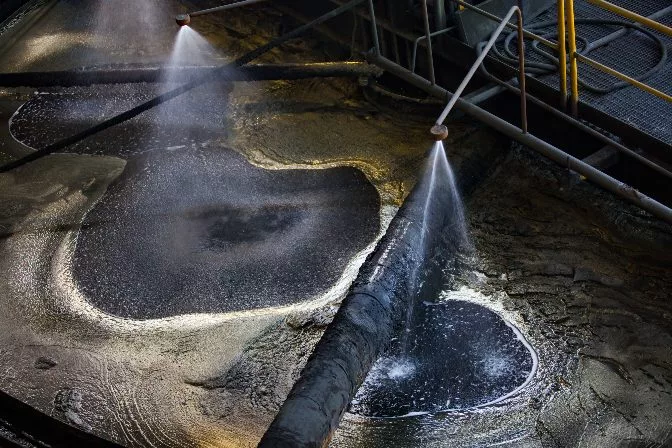
2. Application Areas in Mineral Processing
The main applications of sodium sulfide in mineral processing focus on the separation and purification of ores, such as copper, zinc, nickel, molybdenum, and precious metals:
Copper and Zinc Processing: Sodium sulfide’s primary role in copper and zinc processing is as a flotation agent to regulate ore surface properties, promoting mineral adhesion to bubbles and achieving separation. It significantly improves zinc recovery. For example, in the flotation of copper-zinc polymetallic ores, using sodium sulfide to adjust the chemical environment of the slurry can selectively float zinc minerals. Data shows that copper and zinc processing represents approximately 40% of sodium sulfide applications, with an annual growth rate of 5.2%.
In the flotation of copper-zinc ores, manufacturers using sodium sulfide can improve zinc recovery rates by over 15% while reducing copper impurity content. The separation efficiency for copper and zinc varies depending on sodium sulfide dosage and reaction conditions. By controlling the amount added, selective separation can be effectively enhanced.
Precious Metals Extraction (e.g., Gold and Silver): In precious metal extraction, sodium sulfide is primarily used to regulate slurry pH and stabilize metal ions, optimizing gold and silver recovery. In gold and silver processing, sodium sulfide alters mineral surface chemistry, which facilitates flotation and can also be applied in leaching to increase recovery rates. Processing precious metal ores accounts for around 25% of sodium sulfide applications, with a growth rate of 4.7%.
In gold flotation trials, pre-treating with sodium sulfide can increase gold recovery by approximately 12%, with notable improvements in silver flotation selectivity. This has made sodium sulfide a common reagent in gold and silver mining, especially effective for low-grade ores.
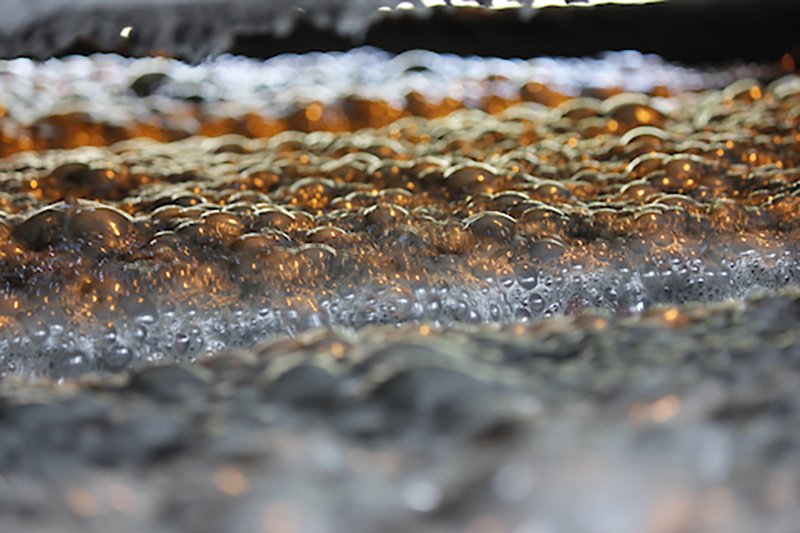
Nickel Processing: Sodium sulfide is used in the flotation of sulfide nickel ores to inhibit sulfide impurities, enabling more effective separation of nickel minerals. Nickel processing accounts for 15% of sodium sulfide applications, with an annual growth rate of 4.3%.
Data shows that adding sodium sulfide in nickel flotation can significantly increase nickel recovery by about 10%, particularly in low-sulfide nickel ores, improving nickel concentrate quality.
Molybdenum and Tungsten Processing: Sodium sulfide also plays an important role in molybdenum and tungsten processing. In molybdenum processing, it acts as a selective inhibitor, helping separate molybdenum minerals from other impurities; in tungsten processing, sodium sulfide adjusts slurry electrical properties, promoting tungsten flotation. Molybdenum and tungsten processing represents 10% of sodium sulfide applications, with an annual growth rate of 3.9%.
In molybdenum flotation trials, using sodium sulfide improved molybdenum concentrate purity by 5-8%. For tungsten flotation, adding an appropriate amount of sodium sulfide increased flotation efficiency by about 9%, achieving a tungsten concentrate recovery rate of over 90%.
Other Minerals (e.g., Lead, Rare Earths): In lead and rare earth mineral processing, sodium sulfide helps adjust mineral surface charges, promoting selective separation of specific metallic minerals. Although lead and rare earth processing represents a smaller demand for sodium sulfide (approximately 10%), demand is rising for complex ore processing.
Data shows that using sodium sulfide in lead processing can increase lead recovery by about 7%. In rare earth processing, sodium sulfide effectively removes impurities such as iron and aluminum, increasing rare earth purity by around 10%.
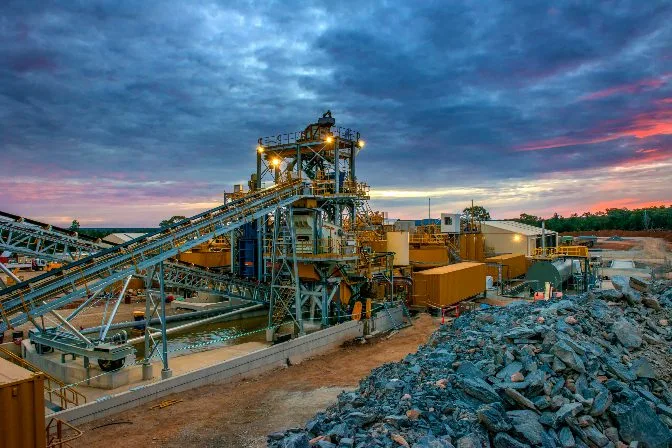
3. Data on Sodium Sulfide Applications in Mineral Processing
The table below displays demand data for sodium sulfide applications across various mineral processing fields:
Data indicates that copper and zinc processing accounts for the largest proportion of sodium sulfide applications. With rising environmental standards, demand is also increasing for low-impurity, eco-friendly sodium sulfide products.
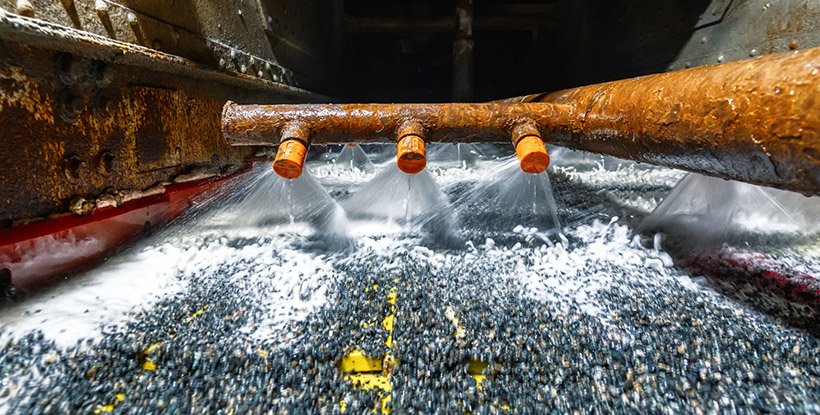
4. Emerging Technologies in Sodium Sulfide Mineral Processing
With continuous technological advancements, sodium sulfide applications in mineral processing are being optimized. For instance, new compound reagents incorporating sodium sulfide have been introduced, significantly enhancing recovery rates for complex ores. Researchers are also developing more efficient sodium sulfide derivatives to improve flotation performance while reducing environmental impact.
Additionally, the push for green chemical solutions is driving the mineral processing industry to explore eco-friendly alternatives. Although sodium sulfide remains critical in current applications, creating environmentally friendly flotation reagents is a vital direction for future industry development.
5. Market Demand and Growth Trends for Sodium Sulfide
According to the latest market reports, the global sodium sulfide market is projected to reach $2.36 billion in 2024 and grow to $5.08 billion by 2034, with an average annual growth rate of 4.8%. This growth is primarily due to sodium sulfide’s extensive use in industries such as mining, paper, leather, textiles, and water treatment. Mineral processing remains one of the largest application fields, and with increased mining activities and demand for mineral resources worldwide, sodium sulfide demand continues to rise, especially in emerging markets like China and India.
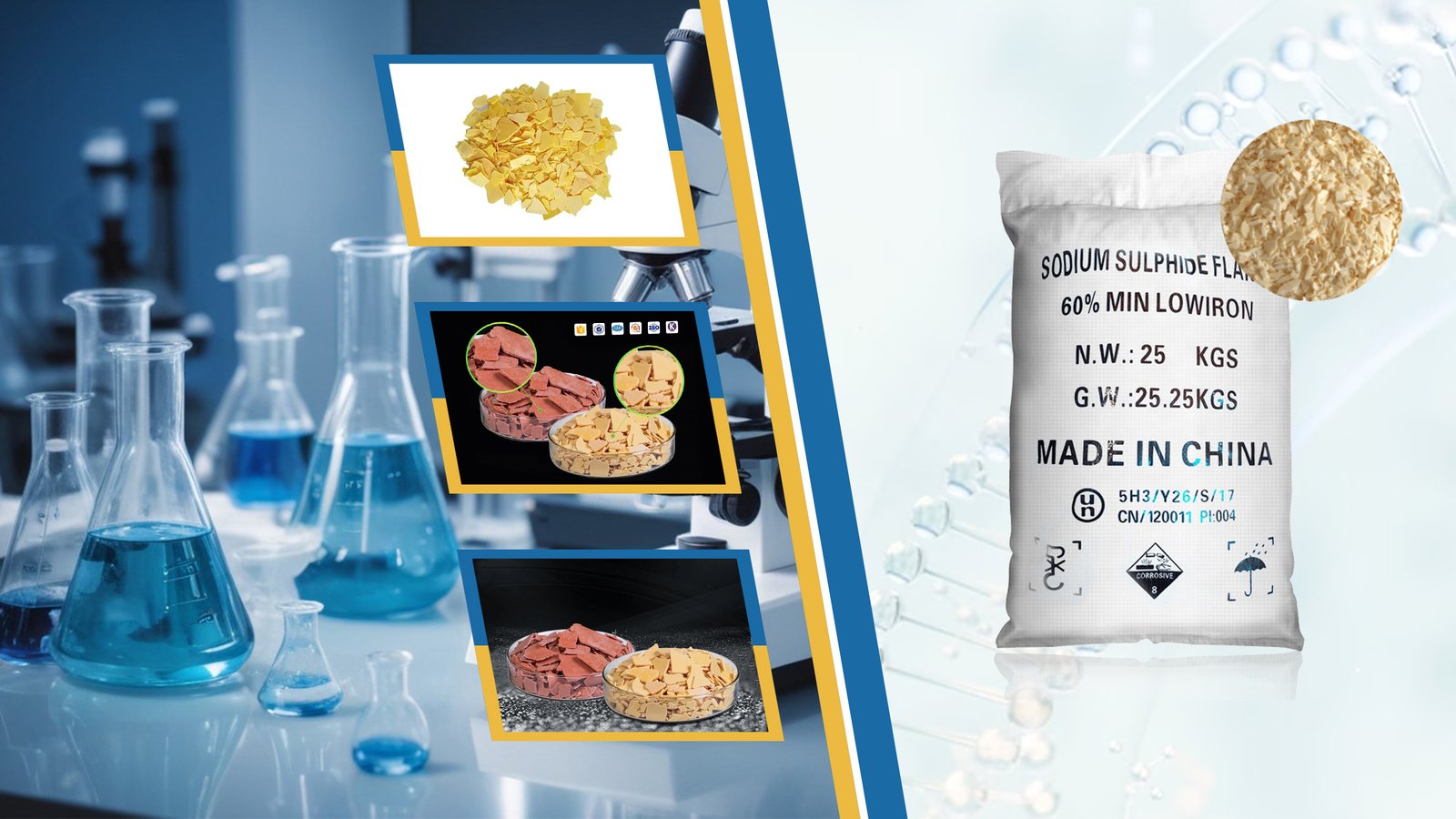
6. Technological Innovation and Development Directions for Sodium Sulfide
Current production technology for sodium sulfide is continually being refined to enhance its purity and environmental performance. Some companies are researching ways to reduce byproduct generation, minimizing pollution during production. Custom formulation services are also becoming a competitive edge for some chemical companies, with quality and cost control as key factors in market share.
In terms of innovation, although sodium sulfide has a wide range of traditional applications, researchers are also exploring its potential use in battery manufacturing. For example, sodium sulfide is gaining academic interest as a solid electrolyte in new all-solid-state sodium batteries.
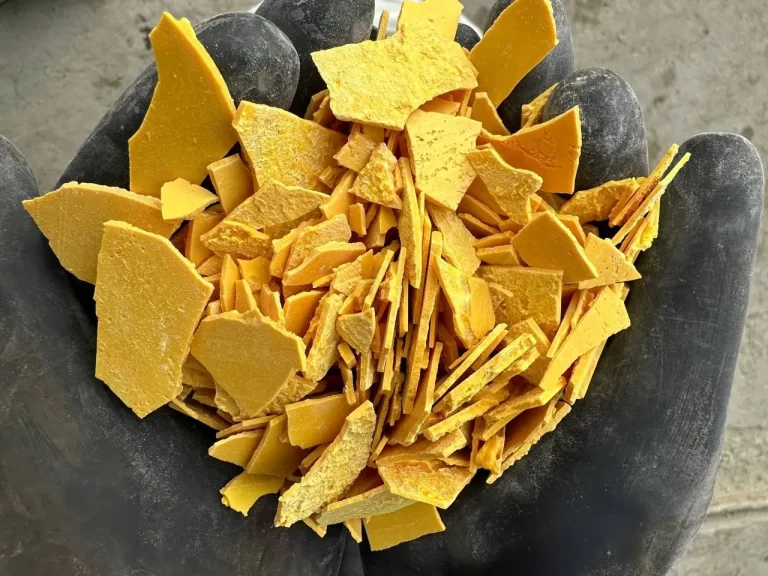
7. Conclusion
In summary, sodium sulfide plays a significant and growing role in mineral processing, with strong market potential driven by technological innovation. With global demand for mineral resources, especially in key minerals such as copper and lead-zinc, the sodium sulfide market share is expected to rise. Mineral processing companies should monitor sodium sulfide-related technological advances and market trends to ensure efficiency and sustainability in their production processes.
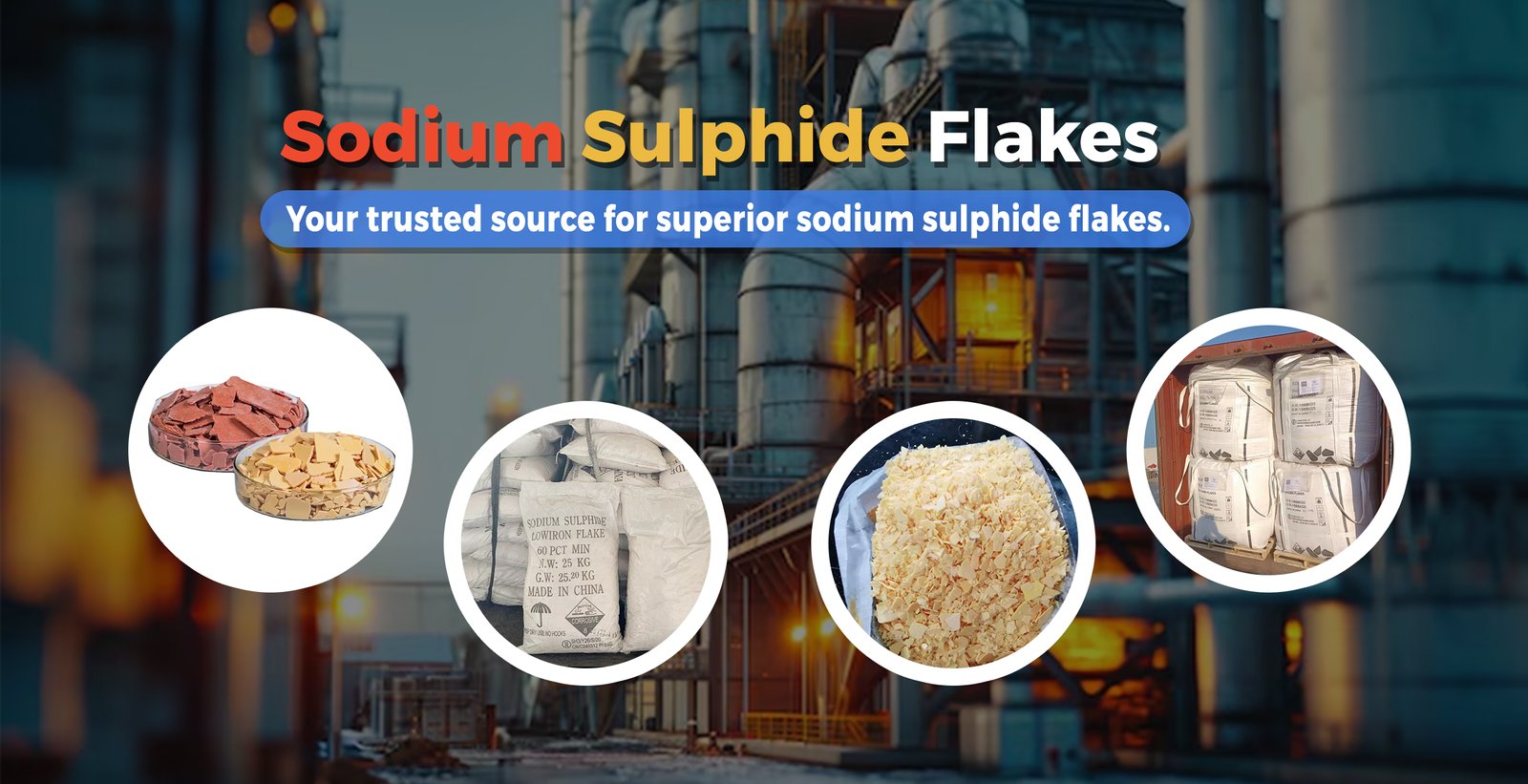
Resource Link: More About Sodium Sulfide